Building high-performance yachts is all about listening for how owners define their perfect day on the water and matching best design, methods, and materials to that intent. Boston Boatworks has taken this Building Excellence approach towards our custom-level quality performance yachts for nearly 30 years.
We have curated from this body of work the best solutions for the new Boston Boatworks Offshore Express Cruiser Series, which prioritize offshore safety, comfort, and range. These designs appeal to the performance-minded owner/operators we love building boats with. It is the boat we’ve always wanted to build and the one our customers urged us to develop.
For an owner/operator who enjoys sharing the experience of time on the water with family and guests, passenger comfort and safety come first on the list of high-performance traits. We know owners who frequently use their boats to travel further and stay out longer. They are likely to be out when the weather turns coming home from the beach or crossing an open water passage to reach an idyllic anchorage. These are the times when ISO CAT A Ocean-rated capabilities and a hullform optimized for express offshore cruising make everyone feel at ease and enjoying the natural surroundings.
Engineering for toughness, durability, and fuel efficiency promotes a myriad of other benefits that knowledgeable boaters appreciate. Building with advanced materials, using CAD design, and manufacturing processes to take advantage of limited series production efficiencies contribute to the custom-level quality of Boston Boatworks-built boats.
We know that high-performance means different things in different situations. For the new Boston Boatworks 44 Offshore Express Cruise, high-performance means high-trust. High-comfort. High-efficiency. Prioritizing offshore safety, comfort, and range is the goal, with owner and passengers feeling at ease enjoying time on the water together, even when the weather turns, even when they are far from home.
Common to all Boston Boatworks best-built boats is our proprietary lamination process, developed over three decades, that optimizes stiffness, strength, and durability with minimum weight. We choose to laminate with two-part aeronautic epoxy laminating resin for its durability and adhesive properties. There is a reason that aircraft are built with epoxy and not any vinylester. Epoxy stretches more than the fiber reinforcement materials do, and therefore will not fatigue. Beyond that basic difference, ensuring precise control of resin content is key to optimizing high-performance laminates.
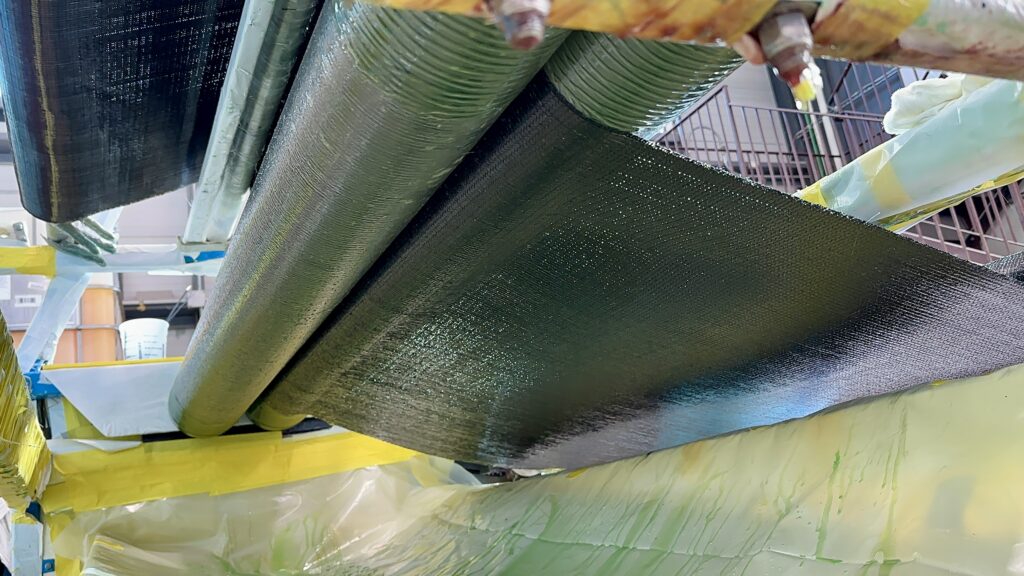
Aerospace ‘pre-preg’ composites combine resin and fiber in the optimal ratio. Shipped on a refrigerated roll, pre-preg reinforcement fabric can be stored for future use.
Our pre-impregnated epoxy composite process uses a specialized roller press to emulate the aerospace pre-preg process without the aerospace price premium. We mechanically force resin into the fiber tows of reinforcement textiles and squeeze out excess to create our own rolls of ‘small batch pre-preg’ cloth that we use immediately, with up to 12 hours of working time.
A specially formulated aeronautic high-performance epoxy resin is used for its superior mechanical properties as a stiff, strong adhesive, ideally suited as a matrix to confine high-performance reinforcement fibers. This high-elongation epoxy is impervious to osmotic damage from immersion in water. It stretches more than the reinforcement fibers and will not fatigue over time.
The two-part resin is mixed, and our roller press process mechanically forces resin into the fiber tows of the cloth itself and squeezes out excess, uniformly pre-impregnating fiber reinforcements for precise control over resin ratio and thorough fiber wet-out. We know how much resin we are using, and where we are putting it before any reinforcement cloths are even placed in the mold. For the BB44, we chose a sandwich composite structure for the hull with a hybrid laminate schedule that increases toughness and reduces noise on the running surface. For the topsides, internal structure, and all parts aloft, we optimize for weight reduction and stiffness without compromising safety margins.
Variable density thermoformed rigid core is used throughout the hull, rather than sheets of saw-cut, flexible contour core. The pre-impregnated epoxy, vacuum-bagged, and post-cured construction process achieves highest strength to weight ratios. In all ways, the scantlings, process, and equipment meet or exceed the ISO CAT-A Ocean certification requirements.
An example of a CAD automated solution to a labor and time intensive manual process we pioneered over 20 years ago for bluewater performance yachts is foam core thermoforming using CAD-driven adaptive mold technology. The value of thermoformed core over saw-cut, flexible contour core is both in weight reduction and improved mechanical properties of the sandwich composite structure.
Saw-cut, flexible contour core is a sheet stock with deep saw cuts on both X and Y axis to allow it to conform to the curvature of a hull. It has the appearance of being sliced into little blocks that are all attached together in a way that allows it bend and conform to a compound hull shape. The slits open as needed to bend. The open slits fill up with resin in the laminating process, adding weight and reducing the slam-load absorption function of the core in a sandwich structure by interrupting the monolithic core sheet with the hardened core in the slits, which is relatively brittle. This decreases the core’s ability to spread shear forces evenly when the hull encounters slamming loads when pushing through waves of incompressible water in offshore conditions.
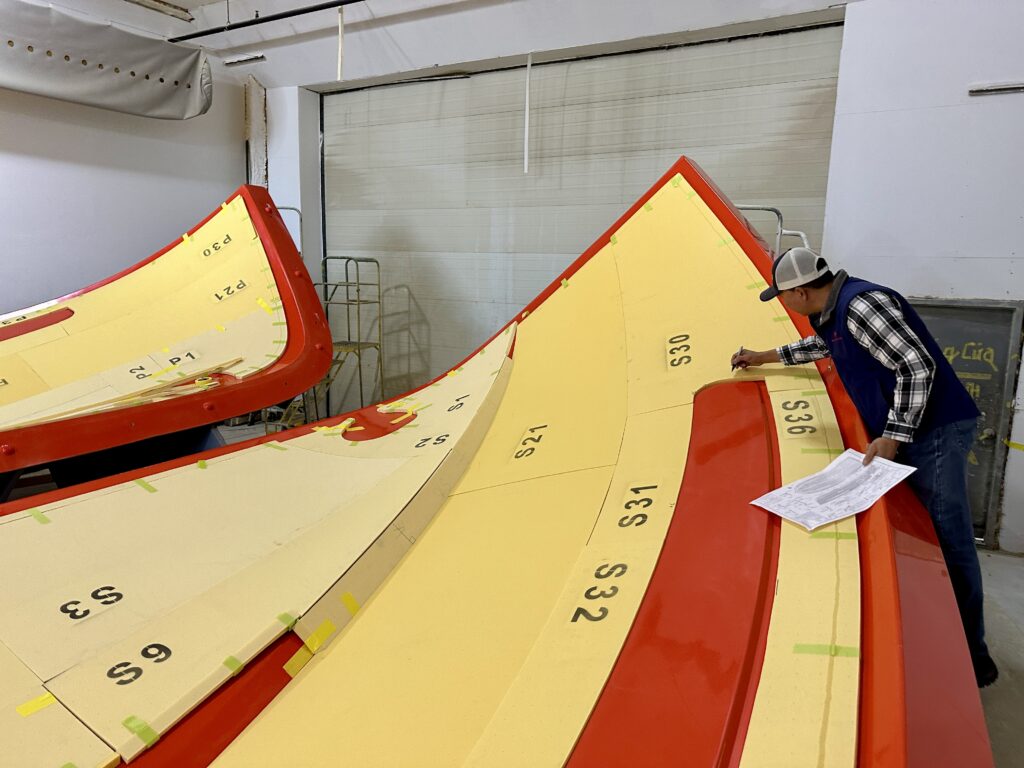
Thermoformed core starts with a flat, rigid sheet of foam with no saw cuts. In the thermoforming process the rigid sheet is heated until it is pliable before bending it to conform with a compound curve of a hull. Thermoformed plain sheets of foam have no kerfs to fill up with resin. Beyond weight reduction and superior structural properties, plain thermoformed core has the additional benefit of improved long-term cosmetic appearance.
For the BB44, built with the efficiencies of limited series production, we turned to BeSpline in Magog, Canada, a specialty composite materials supplier to the aerospace industry.
BeSpline’s innovative CAD-driven adaptive mold technology has automated the thermoforming process. An adaptive mold is a reusable mold that can be deformed from a flat table into any curved shape desired. Programmed with our 3-D CAD model, which controls the precision in the entire BB44 design to program their adaptive mold, can precisely shape individual sheets of rigid core material to create a rigid 3-D shaped core kit, gaining the benefits of our manual process without the excess labor and time requirement. BeSpline vacuum bags a sheet of rigid foam to the flat flexible silicone membrane surface of their adaptive mold, and then heats it until the foam core is pliable. With computer precision, the mold is manipulated by actuators connected by battens to create a fair curve across a compound shape.
Boston Boatworks is the first series built boatbuilder in the United States to utilize BeSpline’s thermoformed 3-D shaped rigid core kits shaped with their adaptive mold technology. We are proud to add BeSpline to our list of industry technical partners and applaud their ingenuity.
In summary, thermoforming is highly effective in reducing weight by eliminating resin uptake and boosting slam-load absorption capability of the hull structure while improving long term cosmetics. Modern manufacturing techniques have made this accessible to series-built luxury yachts.
High-tech composites make better express motoryachts that are fun to drive, with greater safety margins, durability, and increased fuel efficiency. We wanted those advantages for our customers, and it was an easy transition to building best-built express cruisers from our early days of constructing one-off grand prix sailboats. Knowing that the superior properties of epoxy-composite construction means the boats we build will last indefinitely impacts our choices for timeless designs and the best methods and materials used in the rest of the build.